Sprockets are an extremely common and useful gear used in everyday applications, such as bicycles and motorcycles. Some of the earlier automobile models even used them, taking inspiration from the mechanics of bikes!
A sprocket transmits rotary motion by locking its many teeth into a chain and driving it and therefore moving any other parts also connected to said chain. Sprocket gears can have multiple strands, meaning they can attach to multiple different chains at once, and have anywhere from 17 to 114 teeth. Anything above or below those numbers are inefficient.
Sprockets can either be made with or without hubs. Hubs are the thickness seen on either face of the sprocket and are separate from the teeth. The thicker the hub, the more torque the sprocket can transfer.
There are a few types of sprockets, each needed for different applications:
· Type A: These are flat with plain bores. This means they have no hubs at all.
· Type B: These sprockets have only one hub on one of their faces.
· Type C: These have two hubs, one on each face of the sprocket, and they are both equal in their thickness.
· Type D: These sprockets also have two hubs, one on each of its faces, but one is thicker than the other, offsetting it just like a Type B sprocket is offset.
If the wrong kind of sprocket is used (i.e. if its hub is too thick to fit snugly against equipment, or if its number/thickness of teeth don’t match with a chain’s tooth pitch), the entire chain assembly can fall apart, or cause time and money consuming shutdowns.
Sprockets pose a unique challenge when it comes to finishing them properly.
These big-or-little gears require intense attention to detail, which is vital for their function, but time consuming and costly. Normally, a sprocket would have to be deburred, chamfered, and brushed by hand or in a manual machine. These options are fine in some scenarios, but for a production business, these options will ultimately slow you down and disrupt the flow of operations.
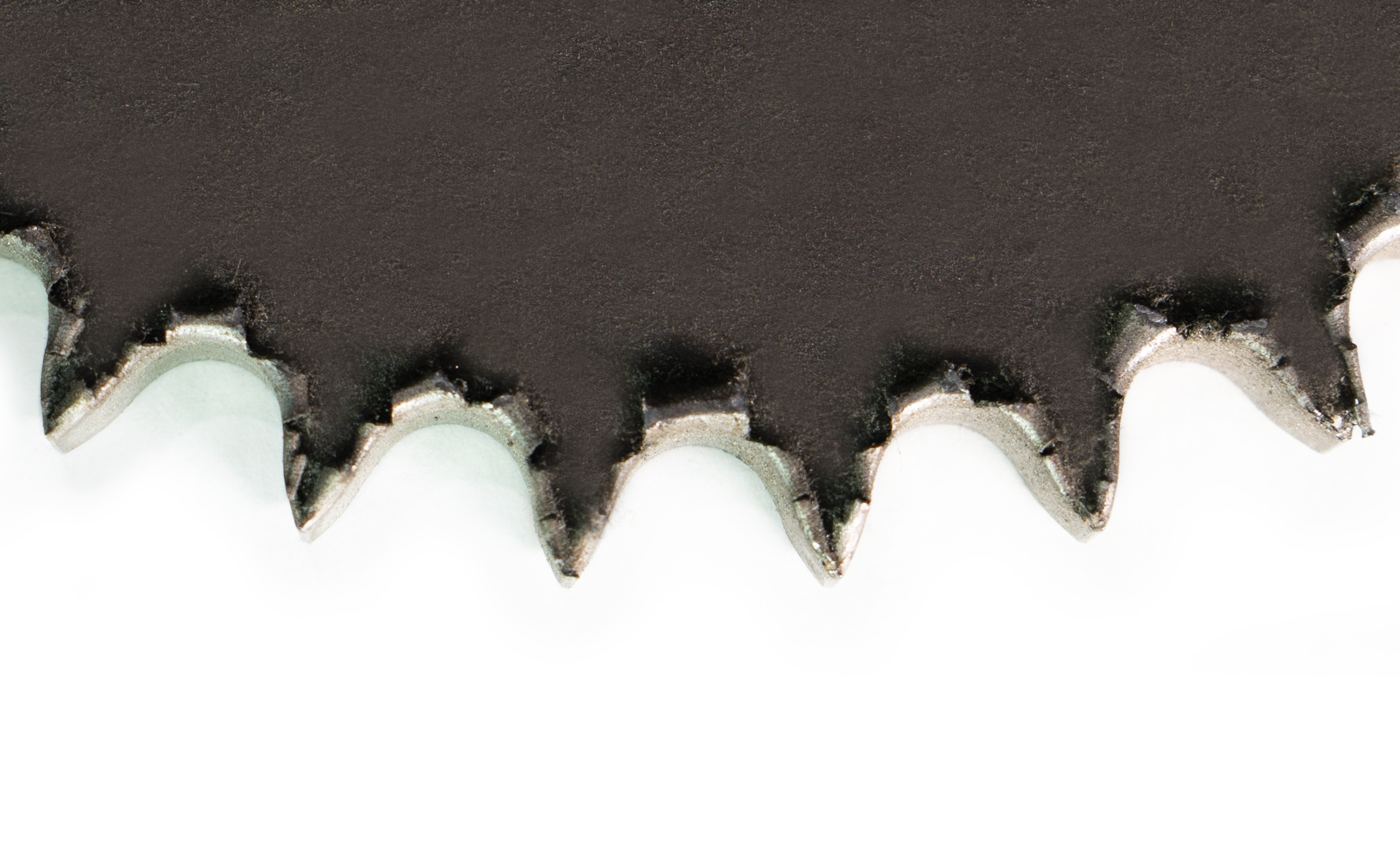
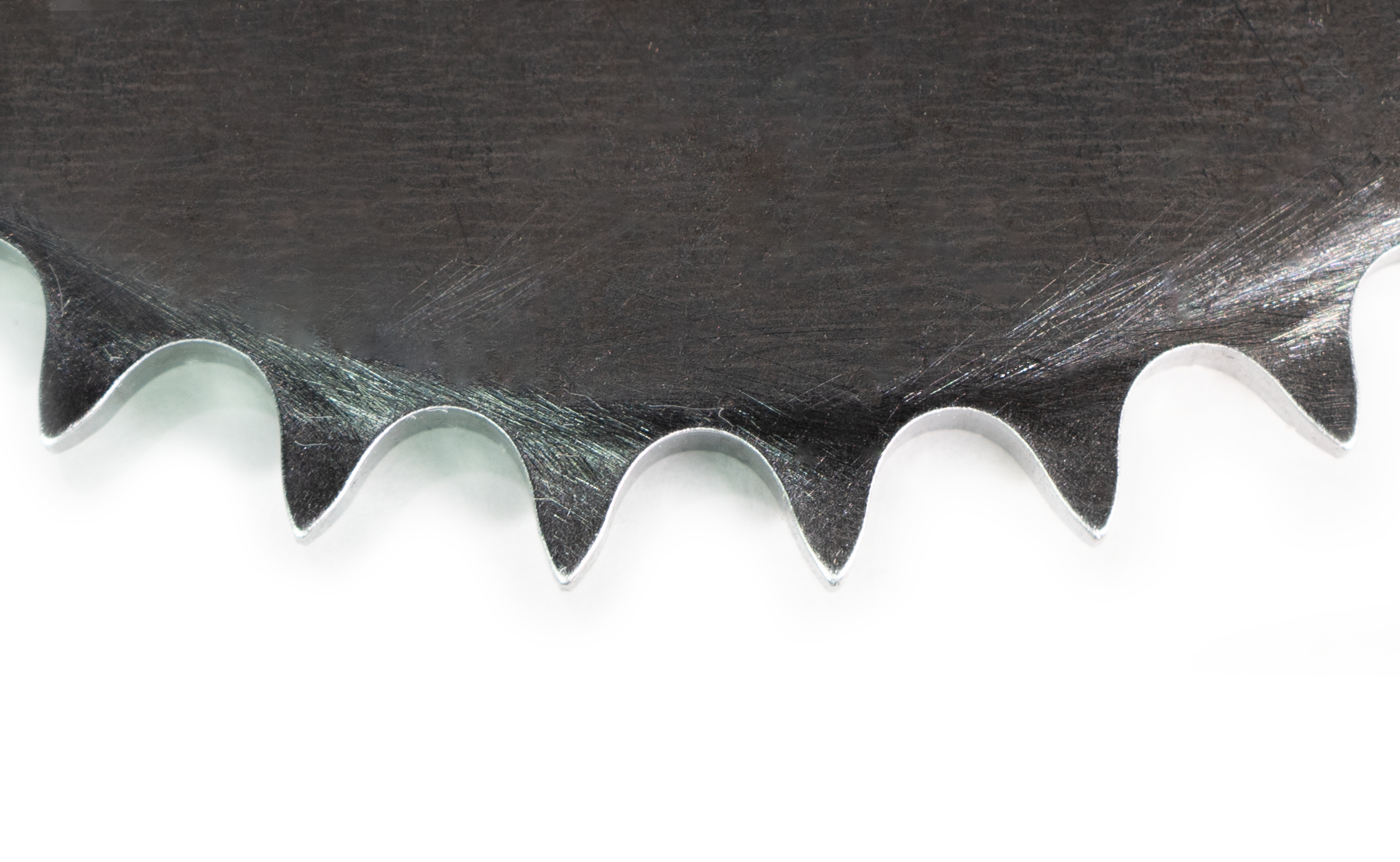
A machine such as the MAX System greatly outpaces any manual and hand operations, especially when sprockets are involved. The MAX will process a sprocket of any size in up to 10 seconds. Two major features of the MAX allow for this amazing processing time: its capabilities to run multiple tools concurrently, and its ability to program part adjustments for future use.
The recipe programming of the MAX singlehandedly makes it a standout machine. It will take operators anywhere from 5 to 10 minutes to adjust the machine to a specific part, and once they have, the MAX will remember said adjustments and save them for future use. It can save a multitude of different part recipes, making it ridiculously easy to change out parts, no matter how drastic size differences/requirements are between them. Because sprockets are such tricky parts, this saves businesses an abundance of precious time.
The MAX also offers both wet and dry options. The machine will run beautifully either way, so it’s ultimately a matter of preference. However, the wet option is fantastic if you’re worried about flammable debris and how it can affect your machine. The wet MAX comes with rust-inhibiting solution so as to not damage machine or part, and it quickly washes away any debris before it becomes an issue. No debris will ever get caught between the teeth of sprockets of any size.
Sprockets can be a manufacturer’s nightmare, but they don’t have to be. The MAX System by James Engineering is built with efficiency and precision in mind, meaning it can take any sprocket with ease.
Watch the video below to see how all of this works in real-time.
High speed precision deburring for quick production